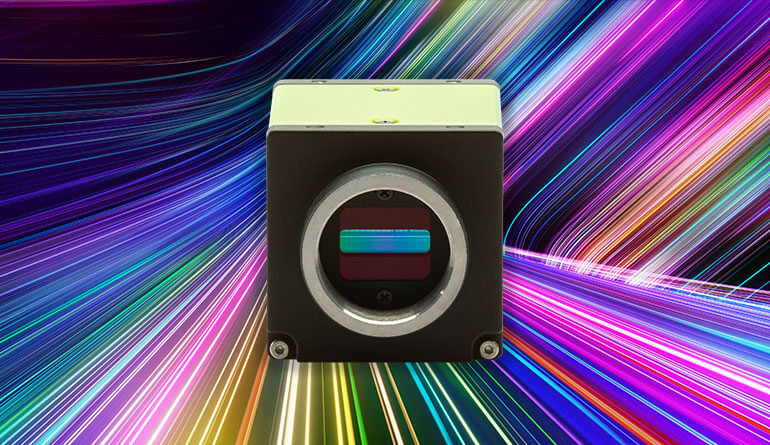
When you’re building a machine vision system that requires high-speed color imaging and has tight space constraints, you can choose between trilinear, bilinear or prism cameras. This blog explains when a trilinear camera is the best choice.
Trilinear line scan camera technology
Trilinear technology uses three separate imaging lines to capture RGB images. In the past, three distinct linear sensors were mounted as close together as possible, but today most newer cameras feature a single sensor with three closely spaced lines of pixels. Each line is equipped with polymer color filters over its pixels to capture one of the three primary colors (red, green, or blue). By synchronizing the camera with the movement speed of the target, the lines captured as the target passes in front of the camera can be combined to create a 2D array of pixels consisting of R, G, and B values.
When is a trilinear camera the best option for your machine vision application?
- When the price of the camera is an important decision factor: Especially now that most trilinear cameras are built around a single, multi-line sensor, trilinear cameras offer a less expensive option than prism cameras. In addition to the lower camera cost, trilinear cameras also offer savings over the recommended lenses needed for prism cameras. Together, this can result in savings of 50% over a comparable prism camera. Be advised, however, that several factors such as the need to use higher intensity lighting and the more rapid degradation of polymer filters vs. prism filters, may negate many of these cost savings over the lifetime of the system.
- When your application requires high-speed imaging: Trilinear cameras are known for their ability to deliver true RGB image data at fast line rates. The latest 2K models (2048 pixels per line) can operate as fast as 44 kHz (44 thousand lines per second).
- When you can guarantee a roughly perpendicular alignment: When trilinear cameras are tilted relative to the target, the distance from the target to each of the three sensor lines becomes different, slightly changing the length covered by each line on the target. If the tilt is small, compensation algorithms in the camera can make adjustments. But for larger angles, the offset can create color fringes (“halos”) or other artifacts in the image. A trilinear camera will perform best when the angle to the target is close to perpendicular and will not require frequent changes.
Need help selecting the right color camera for your application?
Download our Tech Guide: Color Imaging, and walk through the steps of selecting the right color imaging camera for your application.
- When working with a flat surface with minimal undulations: Because the three lines needed to collect full RGB information must be captured at slightly different points in time, ripples or other surface vibrations can cause the target to be closer or farther away when each line is captured. This can create pixel offsets and “halos” as described above. Similarly, discrete objects that might wobble or roll when moving on a conveyor can cause inconsistency between the three lines captured. For best results, trilinear cameras should be used when the target is flat, and any fluctuations are small.
- When all objects in front of it move at the same speed: Spatial compensation is needed to produce sharp edges, as objects pass through the different color lines sequentially. This compensation, based on a reference speed, can achieve edge sharpness comparable to prism cameras. However, when object speeds vary, such as with grains or rice in a chute sorting machine, spatial compensation algorithms cannot fully eliminate halo effects. In such cases, bi-linear line scan sensors have an advantage, as their closely aligned pixel arrays reduce compensation errors compared to trilinear sensors.
- When your system requires a small-sized and lightweight camera with low power consumption: Trilinear cameras are generally smaller than prism cameras which must accommodate the prism and multiple imagers. On top of that, because a prism camera is bigger and has separate control of 3 imagers, it is naturally heavier and requires more power to operate.
Application examples
Here are a few applications where Sweep Series trilinear cameras are especially suitable:
Sorting of fruits, and vegetables by color,
size, shape, and surface quality.
Quality and grade sorting of wood by color
and grain pattern, color matching on laminates
and other flooring products.
Inspection of color print materials on web
presses including magazines, brochures,
flyers, packaging, etc.
High-speed inspection of roll-based products
including colored films, plastics, textiles,
roofing materials, and more .
Color uniformity on wafer surfaces, patterned
wafer inspection, and other wafer/IC defect inspections.
Sorting of small parts by color, checking of
resistor values, inspection of wiring and
component placement on printed circuit boards.
Inspection of tiles looking at color uniformity
and flaws in the glace.
Trilinear or prism camera?
Need help selecting the right color imaging camera for your application? Read our Tech Guide: Color Imaging, and walk through several steps to select the right color imaging camera for your application.